
Then you can start drilling! Use a drill for hard materials for this as bolts can have a high tensile strength. The Dormer A117 is suitable for difficult-to-machine materials and steels up to 1600N/mm2, which means that 12.9 bolts can also be drilled. This drill also works well under less stable working conditions such as in a hand drill. This makes this drill ideal for removing a bolt. It is important that you drill as deep a hole as possible, this will reduce the clamping of the bolt in the hole. And in step 4 you want to have sufficient grip with the wire end extractor. In principle, the deeper the hole, the more grip. In the next step we create a center in the milled face. You do this with a bolt centering cutter. The Dormer P101 is ideal for this. This type of burr is specifically designed for this purpose. Why is it necessary to make a center? This makes it easier to drill in the center line of the broken bolt. Otherwise it will be difficult to remove the bolt properly.
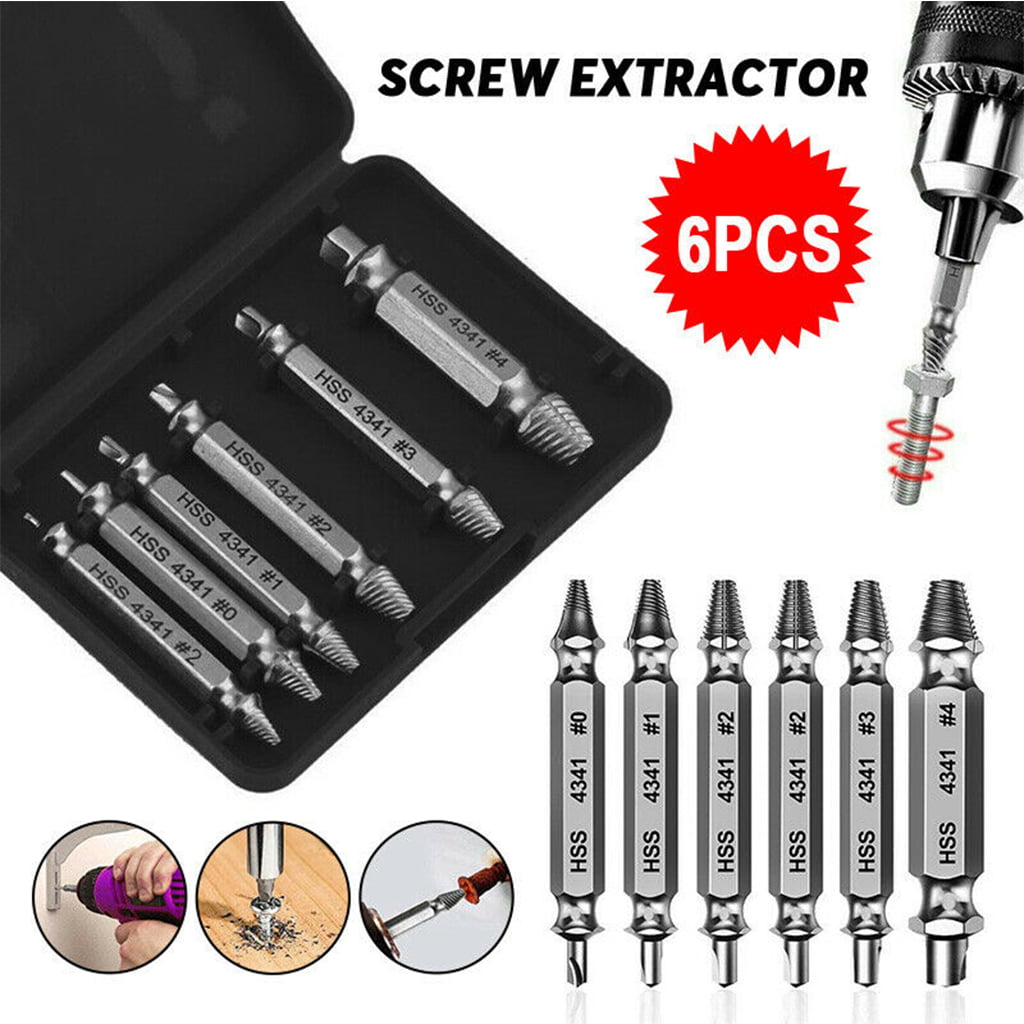
The first step is the face milling of the fracture surface. You can use a bolt face cutter to remove a bolt. The Dormer P100 has been specially designed for this. The bolt face mill works best with a straight grinder. Do you not have access to this? Then another machine will suffice, as long as it has sufficient speed.
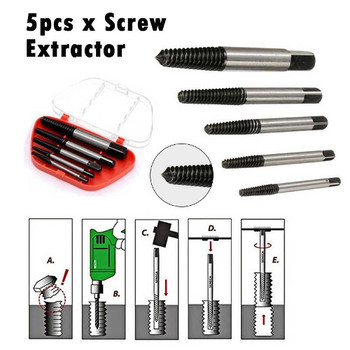
Unfortunately, it happens all too often: a bolt that breaks off in a product. Very annoying. Ideally, you want to solve this problem as quickly as possible. But how do you approach that? You want to avoid further damage to the threads when removing the bolt. Fortunately, there is a simple way to do this. Remove a broken bolt in four steps! Step 1: Face Milling the Fracture
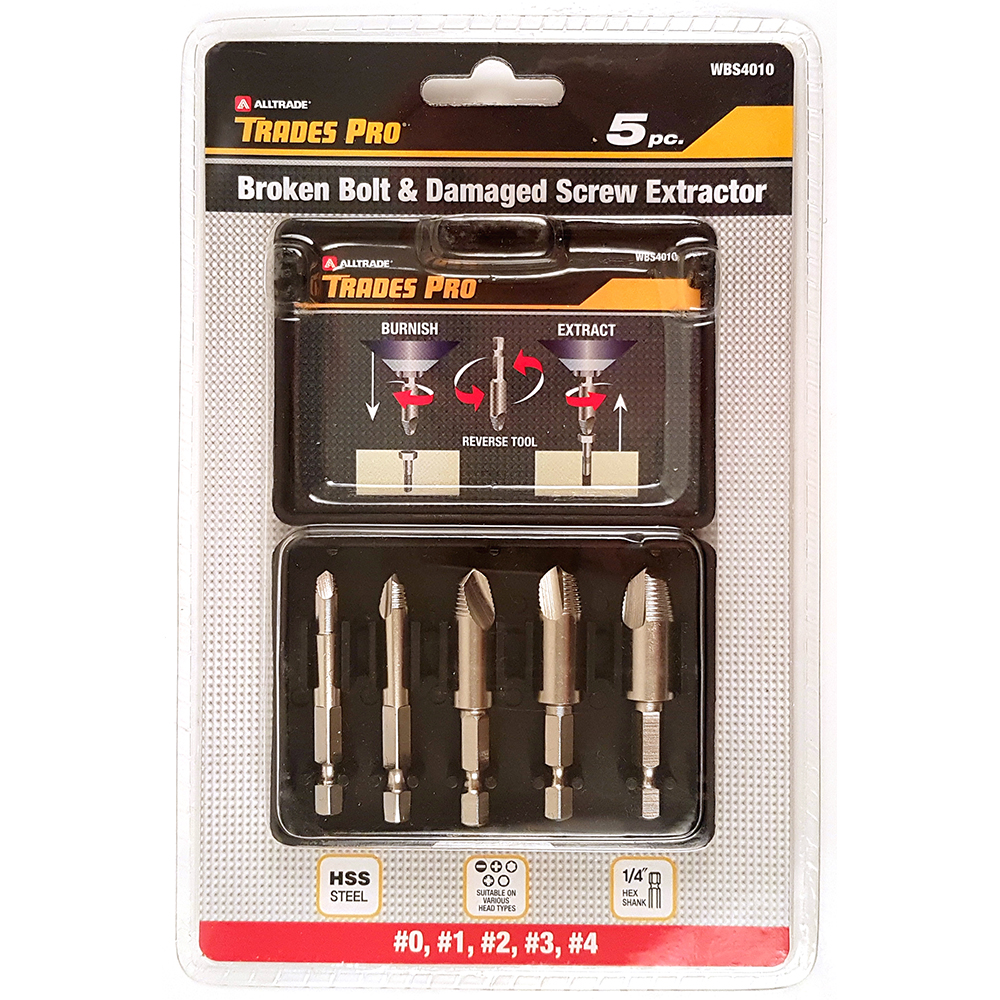
Easily remove a broken bolt: that's how you do it!
